機能
スポット溶接打点の検査をAIで手軽に行う
spGauge 2024.1 の新機能「AI溶接打点検査」のご紹介です。
非接触測定データを使った検査方法で測定の手間や時間を減らすだけでなく、さらに手軽さ・正確性を追求した検査機能をご提案します。
溶接打点位置の検査の現状
皆様は普段、溶接打点位置の検査をどのように行っているでしょうか?
現状、一般的には以下のような3通りの方法があり、それぞれに課題があるかと思います。
① 目視で確認する
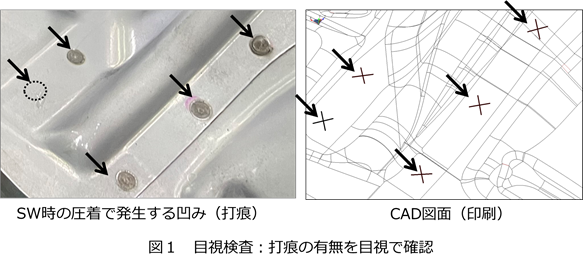
課題→打痕有無が正しいかどうか確認はできるが、位置の正確さはわからない。
② 基準となるエッジからの距離を測り確認する
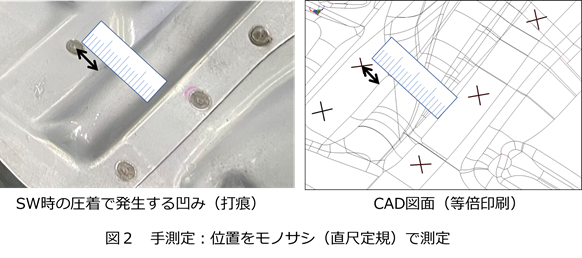
課題→ある特定のエッジとの距離は把握できるが、座標位置での確認ができないため正確性に欠ける。
③ 有接触測定機を使って、目視で確認しながら測定する
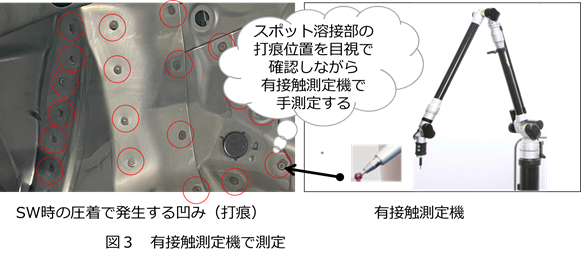
課題→座標位置で確認でき正確だが、手間や時間がかかる。
このような課題から、弊社では非接触測定点群を活用することで溶接打点検査の時間短縮・正確性の向上ができないかとspGaugeの機能開発を行ってきました。
従来までのspGaugeを使った溶接打点検査は以下リンク先をご確認ください。
この機能を使うことで、測定時間の大幅短縮や測定作業者による結果のバラツキ、測定漏れを無くすこと等を実現しました。
しかし、こちらは打痕形状から判定するという機能のため、次のようなケースがあった場合、打痕の凹み形状が測定データでしっかり再現できず、自動検出率が低下するという課題がありました。
ケース1:打痕の凹みが少ない(浅い)
ケース2:3Dスキャナーの形状再現精度が低い
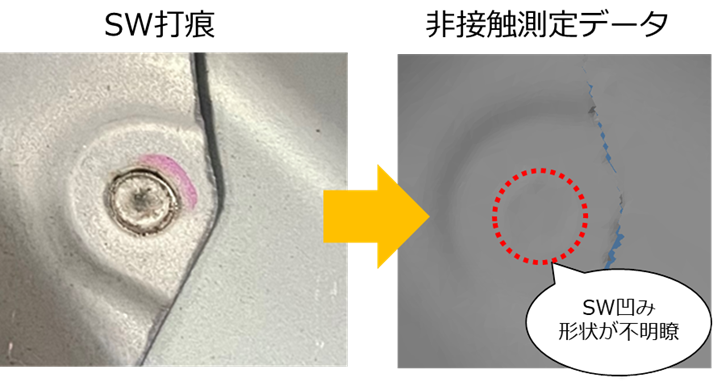
AIを使った溶接打点位置検査で課題を解決
上記の課題を解決するため、打痕に投影した曲率階調色の画像をAIに判別させるという方法で、溶接打点位置の検査をできるようにしました。
それが、spGaugeの新しい溶接打点検査です。
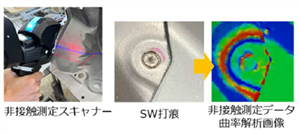
この機能を使うことで、従来の検査機能で20か所出ていた誤検出が、たった1か所にまで減ったというテスト結果もあります。
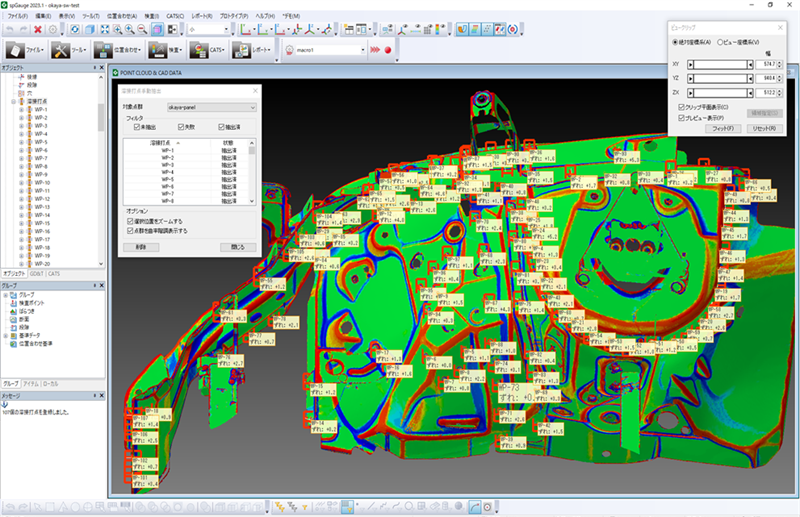
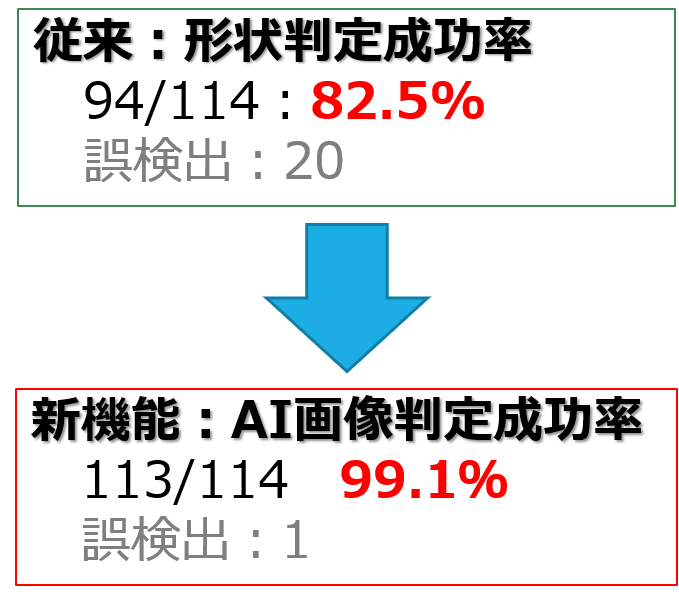
AI溶接打点検査の流れ
それでは、この新しい溶接打点検査の流れをご紹介します。
まず、検査前の準備として3D測定データと3D CADデータ(設計データ)の位置合わせを行います。
そして、3D測定データに曲率階調を投影します。
次に、打痕の候補となる画像を自動で抽出します。これは2Dデータとなります。
予め登録された学習データを使って、自動抽出された画像から打痕位置を自動判定します。
その後、結果を3D測定データへ自動でペアリングし、位置ズレ量(3D CADデータとの比較)を自動で検出します。
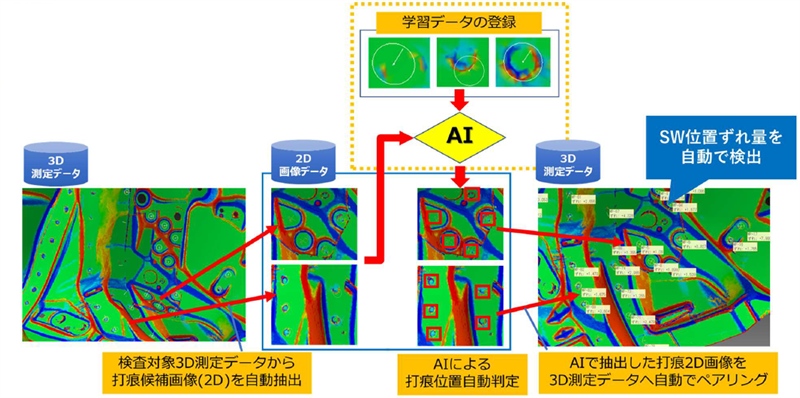
最終的に、レポート抽出も可能です。
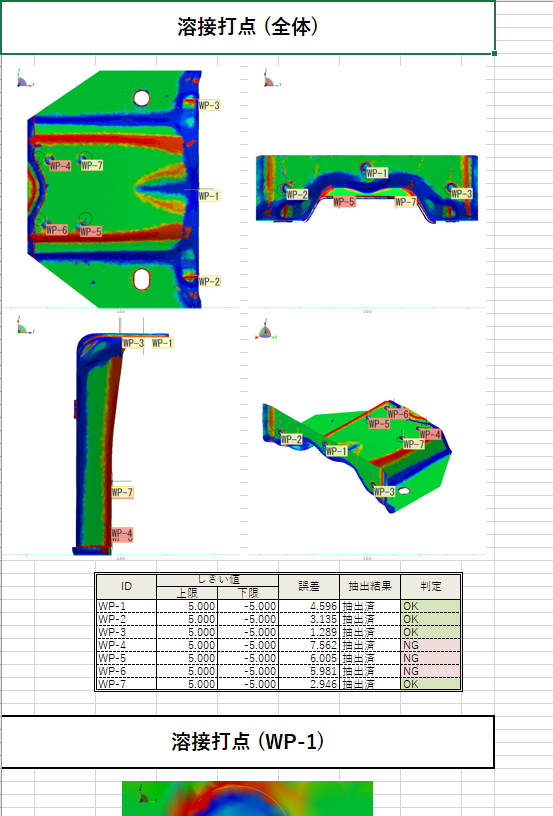
この革新的な機能により、現物の測定から検査、レポート作成まで、従来に比べて格段に時短で、高精度で溶接打点検査が実現します。
是非、spGaugeのAI溶接打点検査機能をお試しください!