Features
Innovative Inspections of Spot Welding Points
Would you like to get rid of errors and oversights when inspecting contact spot welding points?
Mass production uses robots for welding. Prior to mass production, inspections are implemented to check if spot welding points are in the correct locations, and welding locations are adjusted. Usually, during that inspection stage, welds are checked visually, and inspections are implemented using contact-based measuring devices.
Want to eliminate errors and oversights in the contact-based measuring.
Inspections of spot welding points for stamped products are implemented by using contact-based inspections for the center positions in the dozens or the thousands of welds.
With contact-based measuring, all spot welds are identified visually, and then a probe is put in physical contact with the welds to inspect them. For that reason, this process takes quite a long time, and can cause errors and oversights with regard to the inspection locations.
Issues with contact-based measuring
- Long measuring time
- Errors occurred due to variance in the results of inspections conducted by humans
- Oversights occurred due to forgotten measurements
- Oversights occurred due to failure to check spots that should have been welded
- Long re-inspection time taken for occurred errors or oversights
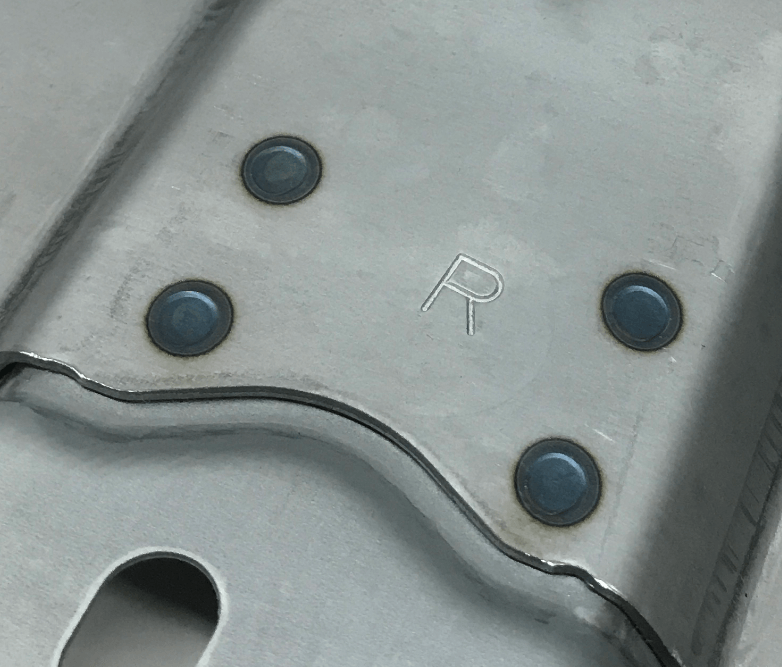
Eliminating oversights by CAD data
If welding point geometry in the CAD data is registered in advance, the welding points will automatically be recognized, which can eliminate oversights.
Spot geometry in CAD data
- Cross: Two intersecting lines
- Point: A point (The normal direction is the direction of the CAD surface.)
- Circle: A circular shape
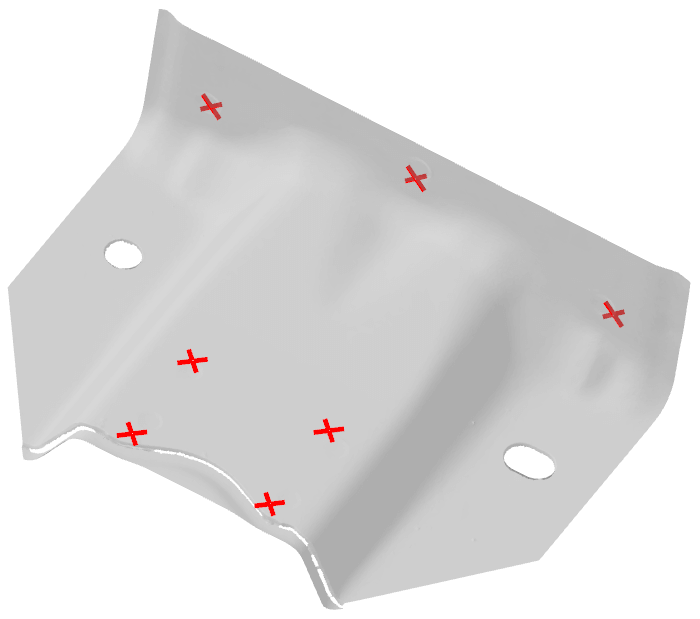
Reducing time and eliminating errors and oversights through automatic inspection
If errors and oversights occur, time is required for re-inspection as well as for the preparations and measuring.
Using spGauge makes it possible to detect welding points automatically to avoid errors and oversights by preparing point cloud data measured by non-contact measurement digitizer for the shapes of which they have been spot welded, as well as the CAD data for spot welding point positions.
Additionally, tight spacing between welding machining can cause welding defects, but spGauge makes it easy to check if proper spacing has been provided for all spot welding points.
Furthermore, even if repeated measurements are needed, the measurement point cloud data can be reused, and analysis can be performed by modifying the conditions with spGauge.
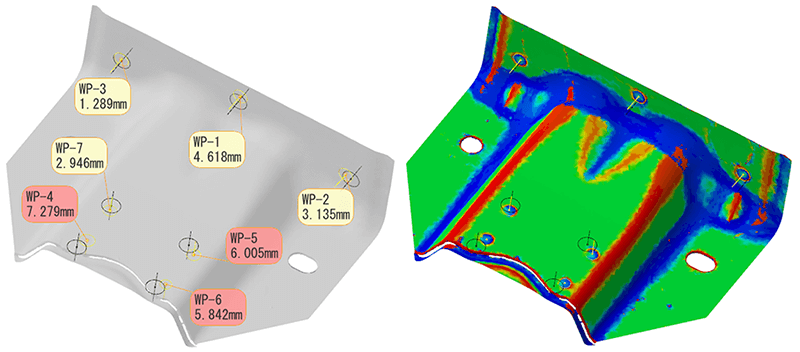
Judging the distances between welding points
If the spacing between welding points is tight, welding defects can occur. Dangerous areas can be detected by checking the distances between all welding points.
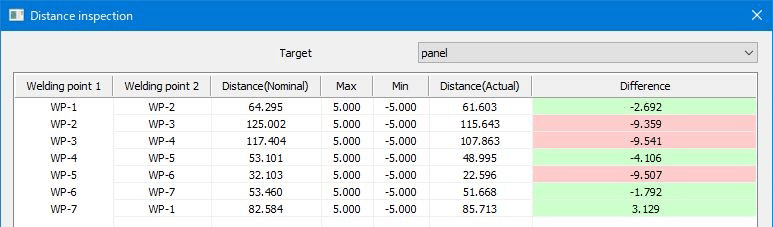
The effectiveness of welding point inspections
Measurement data tallying and checking time is reduced by 50%!
(A) Measurements, data tallies and inspections from 3,000 welding spots performed with contact-based measuring
(B) Shape measurements made by non-contact measuring and spot welding point inspections implemented by spGauge
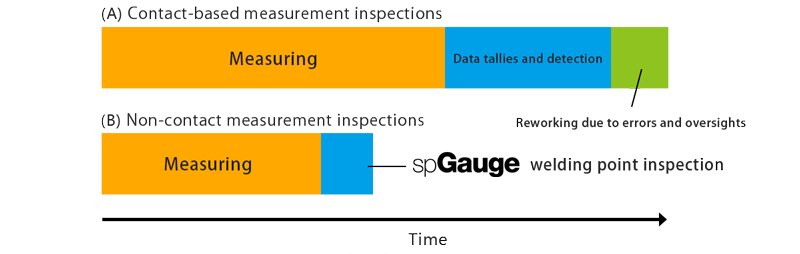
tag : Press Welding point