Reverse Engineering of High-Quality Spline Surfaces
spScan is a reverse engineering tool specialized in creating a NURBS surface from point cloud data.
HOME > spScan
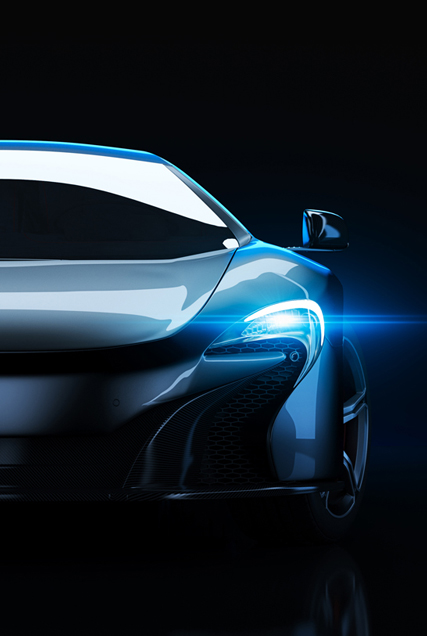
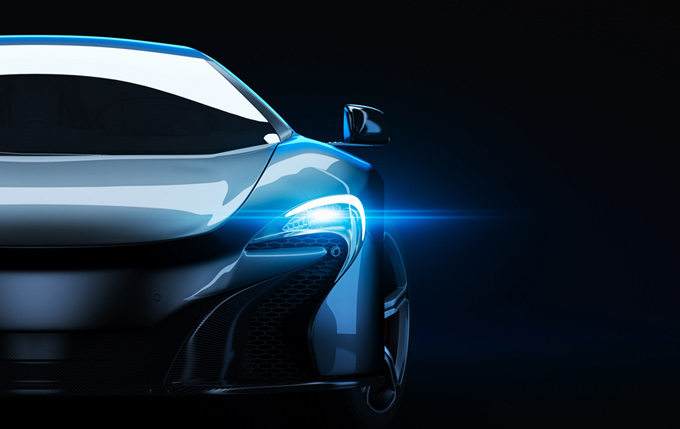
01/03
Create Spline Surfaces that can be Handled Easily by CAD/CAM/CAE
Are you able to use surfaces created with conventional reverse engineering tools for post operation processes such as for design and analysis?
spScan is a reverse engineering tool that can effortlessly create spline surfaces with CAD surface configurations from non-contact measurement point cloud data that are easy to handle in CAD/CAM/CAE.
Display point cloud shape using curvature analysis color map. Using these colors, spScan can distinguish the surface construction and create surfaces (trimmed surfaces) by differentiated colors.
The intended surface can be created readily according to purposes such as to “reproduce a faithful shape with little deviation from point cloud using surfaces” or “create a smooth surface with few control points.”
The created surfaces can be exported in a generic CAD format (IGES/STEP) and can be used in a CAD/CAM/CAE.
Surface data resulting from reversing a solid shape can be utilized in a CAD system as solid data.
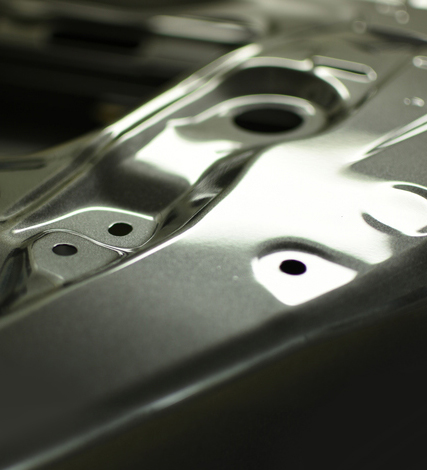
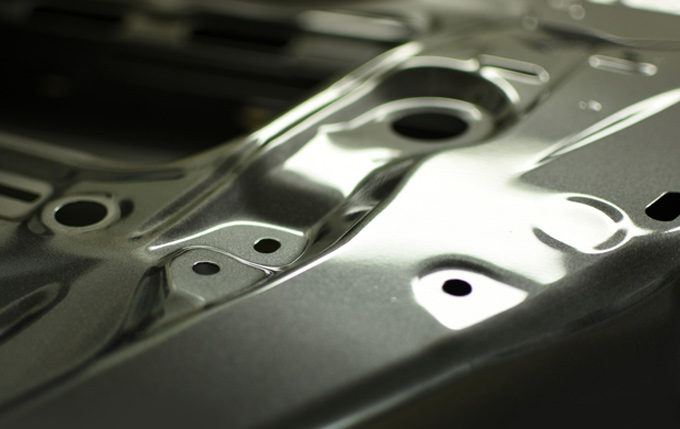
02/03
Drastically Reduce Man-Hours Spent on Reverse Engineering Through Partial Reverse Engineering Features
Are you spending too much time reverse engineering from point cloud?
If a CAD data exists, point cloud data and the CAD data can be compared so that only the surfaces that are different can be reconstructed. Since only the differences are reverse engineered, the man-hours can be significantly reduced compared to reversing the entire model.
In spScan, this is called "partial reverse." In "partial reverse," new surfaces are created so as to be continuous with the surrounding surfaces, while maintaining the tolerable distance.
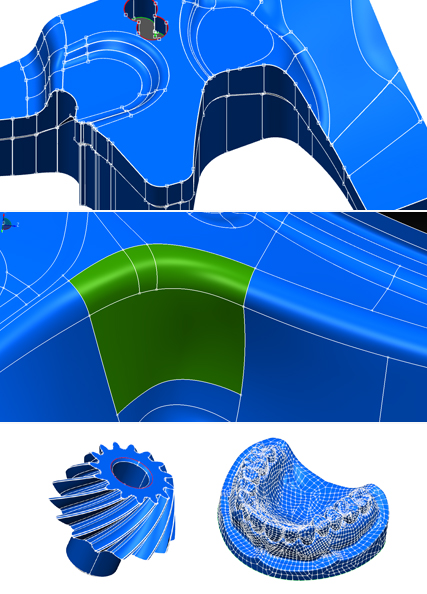
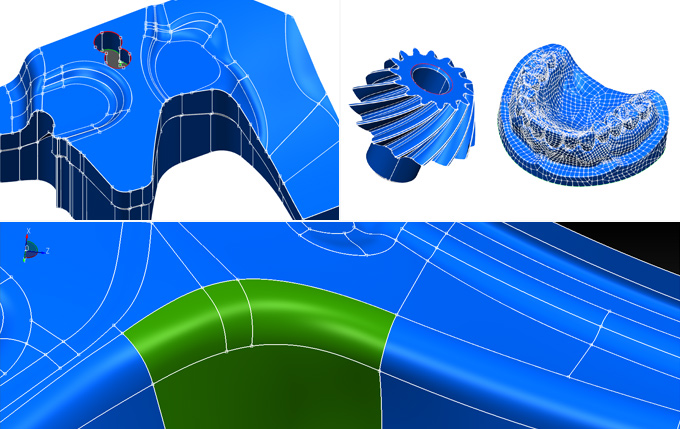
03/03
Reverse Engineering Methods Rich in Variations
spScan has several methods available for reversing as part of standard features.
The method can be chosen according to the reversing purpose and use.
Total reverse: Reverse engineering with point cloud data alone
- Patch surface (four-sided net patterned surface construction) creation
- Simple automatic surface creation using the grouping feature
- Surface creation of CAD surface construction with manual operation
Partial reverse: Reverse engineering with CAD
- Recreate diverted surfaces alone
- Move, deform and fit the diverted surfaces to a polygon mesh
- Fit multiple surfaces to polygon mesh at once