Use cases
Providing Mold Hand-Finishing as Feedback for Design (Mold Copying)
Here is an example of spScan reverse engineering utilized to create mold copies and spare parts.
Problems with creating mold copies
During press mold creation, the accuracy of the stamped product is checked using the mold shape created with CAD software. It is necessary to modify the mold shape until the required level of accuracy is reached in the press product shape.
If, after carrying out the processes of (1) creating the mold, (2) stamping a product, and (3) checking the accuracy of the stamped product, the product accuracy is poor, you return to carrying out further mold modifications. By repeating this process of trial and error (rework), you create a mold that can produce stamped products with good accuracy.
Normally, the shape must be modified using CAD software, but personnel in the die production workplace with many years of experience sometimes change the mold shape manually. In such instances, the manually finished shape was not reflected in the mold’s CAD data.
Because the shape of the hand-finished part of the primary mold is not reflected in the mold’s CAD data, when it comes to making multiple molds (secondary molds) identical to the primary mold for developing production equipment to send overseas or to prepare spare parts, it is necessary to perform mold modifications during secondary mold creation just like the primary mold.
Using reverse engineering to make the mold’s CAD data reflect the hand-finished shape
The hand-finished mold shape is measured using a no-contact measuring device, and the mold’s CAD surface data is made to reflect the hand-finished mold shape by applying reverse engineering technology that creates CAD data from the point cloud of the hand-finished shape.
When comparing the mold’s CAD data with the hand-finished mold’s measurement data and recreating CAD surface data for the hand-finished data only, we also applied the ‘partial reverse engineering’ tool included in spScan to reduce the man-hours required in reverse engineering.
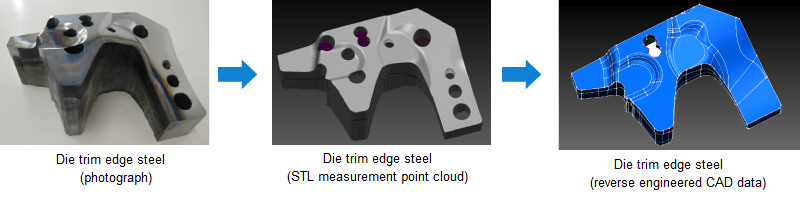
Reducing the cost of creating secondary press molds
- By having the secondary press molds reflect the shape of the primary mold, which was able to product good products, we reduced the number of reworking times required for secondary mold creation.
Reworking times: reduced from six to two
- We reduced the cost of creating secondary molds.
Total man-hours, including design, processing, trials, and inspection, were reduced by 65%
The ability to create reverse engineered surfaces suitable for press applications
- Intersection curves (corners) between spline surfaces can be created.
They can be applied to the creation of 3D profile data for the trim edges of trim dies.
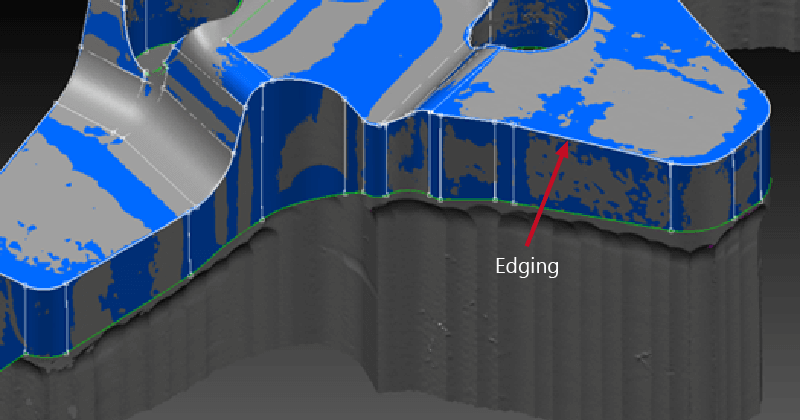
- Non-undercut spline surfaces along the metal stamping direction can be created.
Spline surfaces extruded in the metal stamping direction on the trim edges of trim dies can be created.
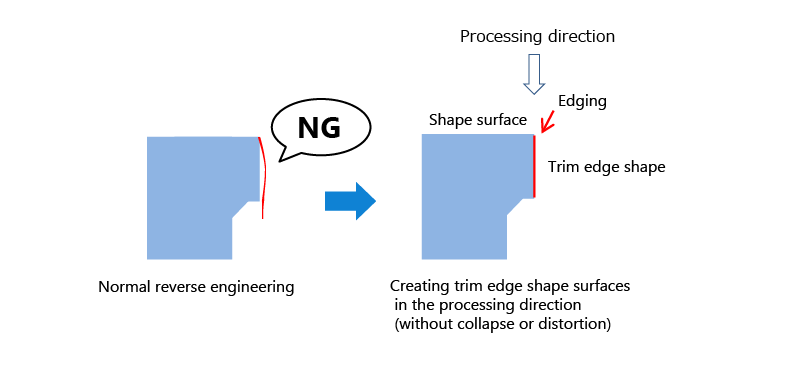
tag : Mold copies