Use cases
Reverse Engineering From Clay Model Designs
Here is an example of spScan reverse engineering utilized to convert a clay model design into CAD data.
Issues with converting clay models to CAD surface data during the initial design stage
In the evaluation of the initial design stage, a model (scale model) of the actual object is created by the design modeler, and the shape is converted to point cloud data using a no-contact measuring device. Furthermore, CAD software is used to create simple CAD surfaces from the clay model’s measurement point cloud, which can be used for examining designs, adjusting functional component layouts, and so on.
Clay models frequently undergo shape changes during the initial design stage, and creating prototype surfaces using CAD software in accordance with those changes takes time. In the past, design examination required more time because the clay model could not be converted to CAD surfaces in a timely manner.
The development schedule would be affected by delays in the initial process of design work, and this tended to cause the schedule for the later process of part design to become tighter. Additionally, there was also the problem of being unable to create spline surfaces that fit the clay model using CAD-based methods of creating prototype surfaces.
Making evaluation during the initial design stage more efficient by creation of CAD surfaces with spScan
- Appropriate use of the multiple reverse engineering methods offered by spScan, including ‘partial reverse engineering’, have resulted in a 60% or greater reduction in the man-hours required in converting measurement point cloud data from the clay model to 3D CAD surfaces during the initial design stage.
- The smooth creation of CAD surfaces using spScan allows for adequate evaluations to take place during the initial design stage, which helps to eliminate the factors of delays in the development schedule.
- It is now possible to create spline surfaces that maintain the accuracy of the point cloud created by measuring the clay model.
Example of curvature displayed from a point cloud obtained through no-contact measurement of a clay model
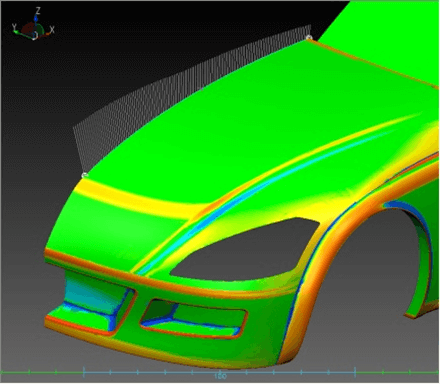
3D CAD surface conversion: illustration of reverse engineering
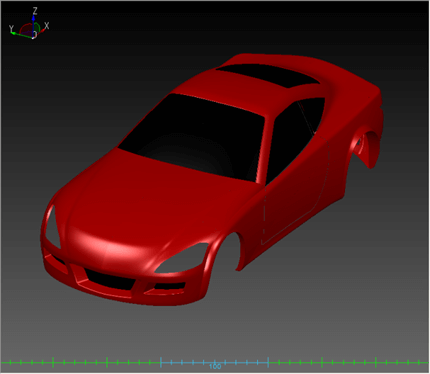